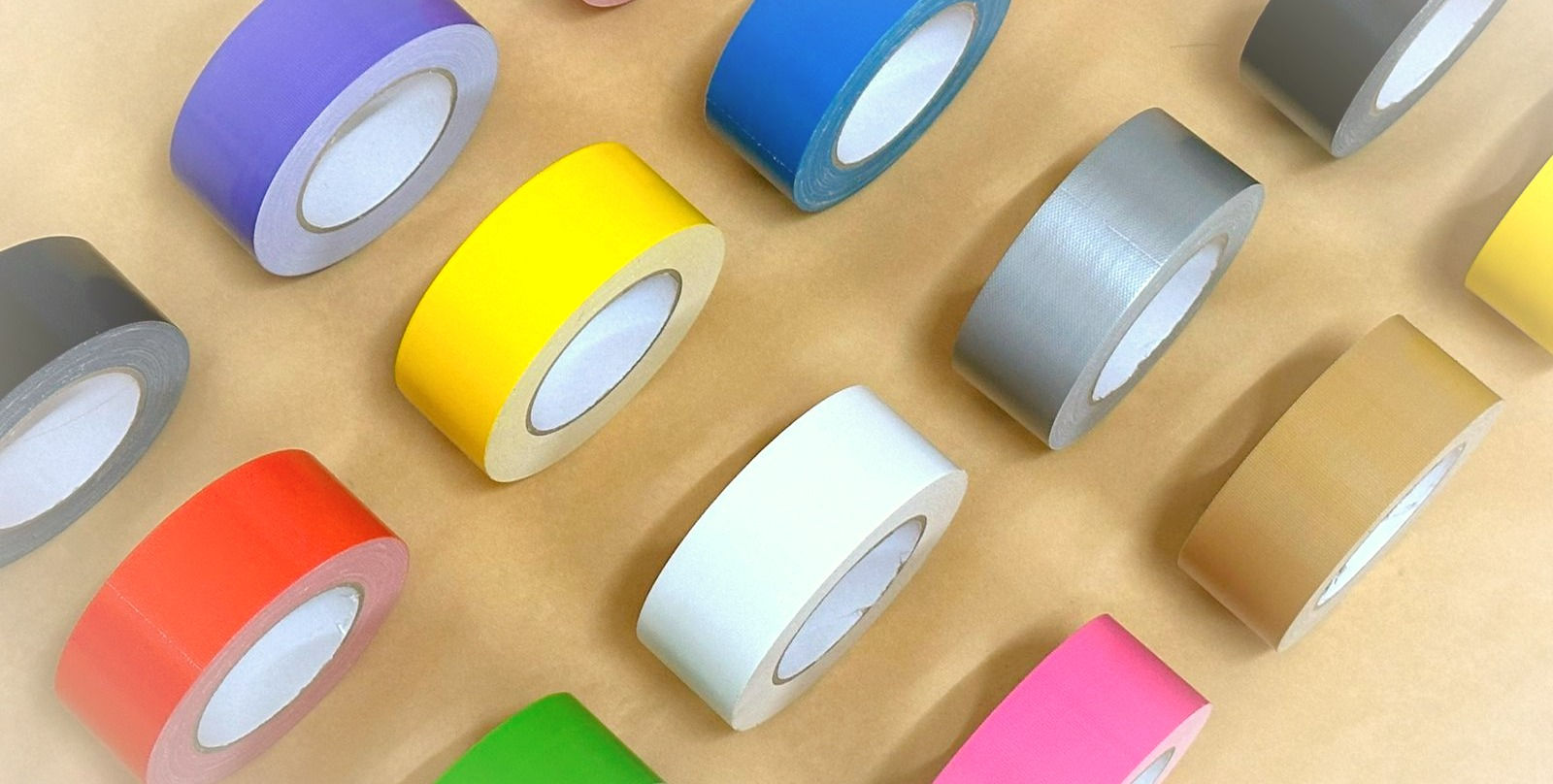


Manufacturing Protocol
At Pt. Okamoto Indonesia, we exercise complete control over every stage of the manufacturing process in-house, granting us vertical integration and unfettered autonomy in ensuring the quality and excellence of our products.

01
Yarn Sizing
The utmost attention is devoted to sourcing the finest threads and yarns from global origins, meticulously prepared to weave the foundational fabric for the production of Cloth Tape.
02
Mesh Weaving
A fleet of 60 meticulously customized air jet looms is actively engaged in weaving the foundational fabric for cloth tape production. These precision-engineered looms cater to various mesh specifications, ensuring a superior quality base material that adheres to the highest standards of craftsmanship in the textile industry.


03
Extrusion Lamination Coating
The foundational fabric undergoes a precise co-lamination process with multiple layers of polyethylene, featuring varied colorants and strengthening additives for enhanced structural integrity and a versatile color palette in the production of cloth tape.
04
Adhesive Mixing / Application
In-house, custom adhesives are precisely formulated for each product and applied with substantial pressure to ensure both proper adherence and uniform distribution in the manufacturing of cloth tape.
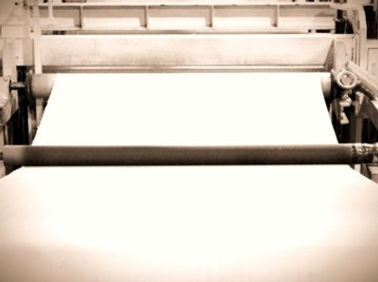
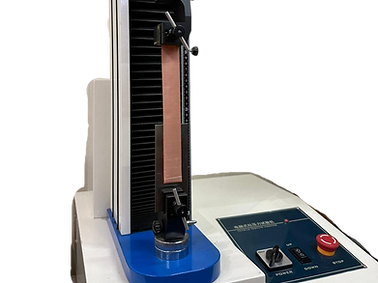
05
Lab Testing / Quality Control
Each production lot undergoes thorough testing in our in-house laboratory, ensuring strict adherence to the highest quality standards for the cloth tape manufacturing process.
06
Cutting, Packaging, Boxing
After precision cutting, each item is custom-packaged based on client requirements and carefully boxed for shipment, reflecting our commitment to tailored solutions and efficient handling.
